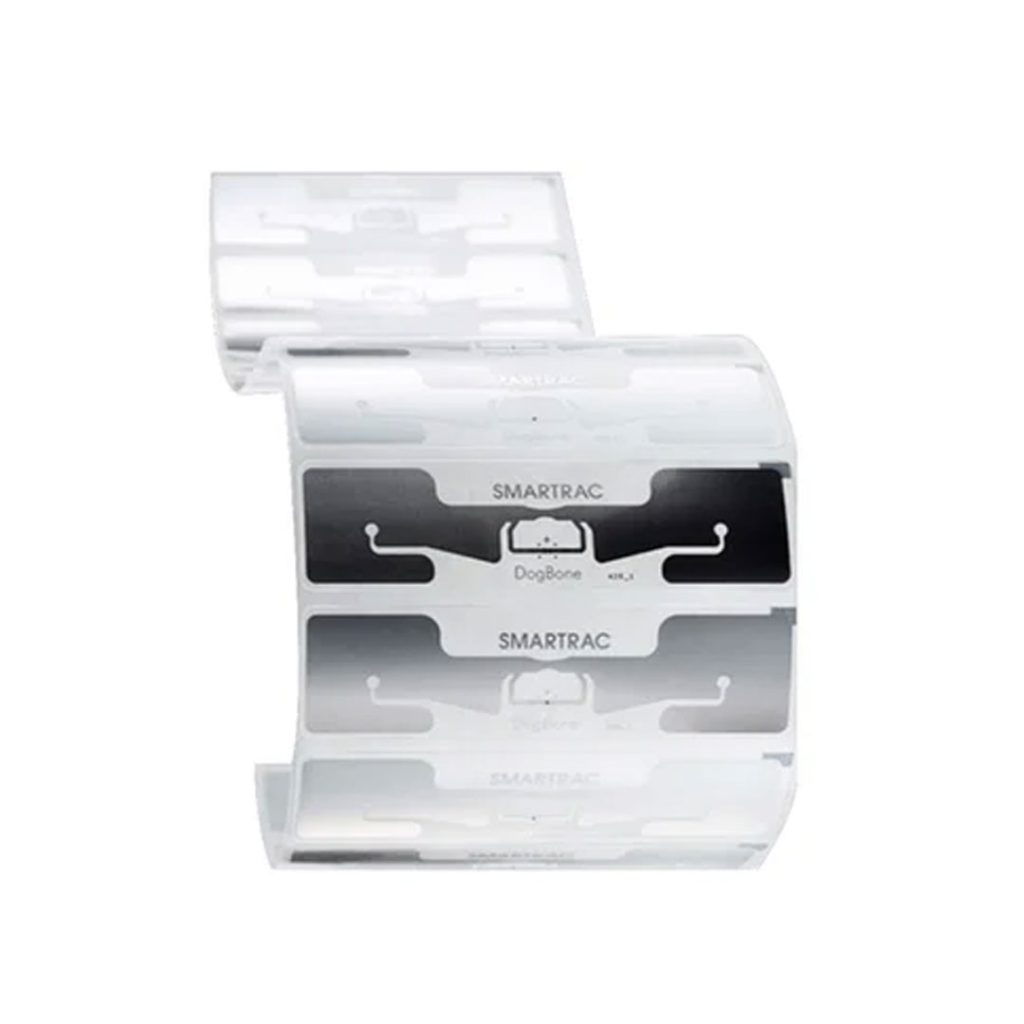
DogBone Inlay RFID Label
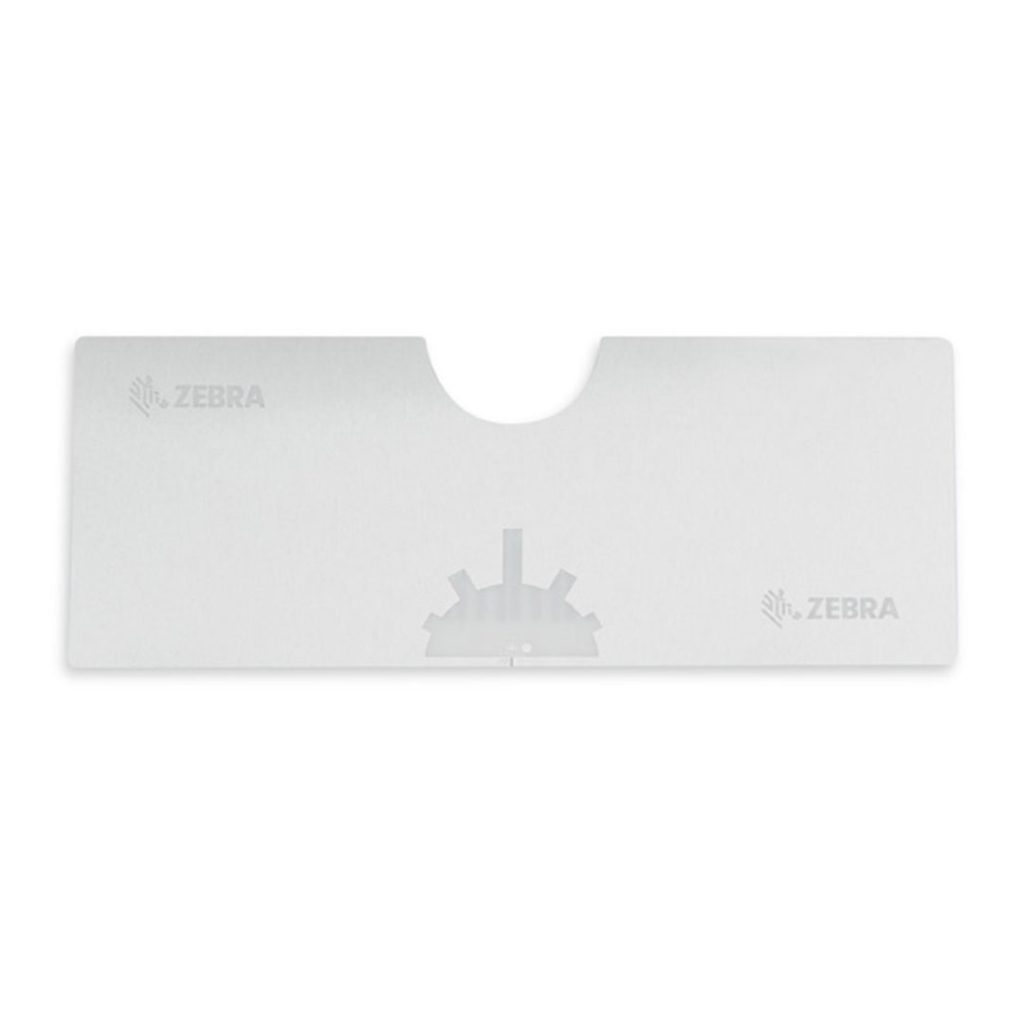
Zebra ZBR4000 Inlay RFID Label
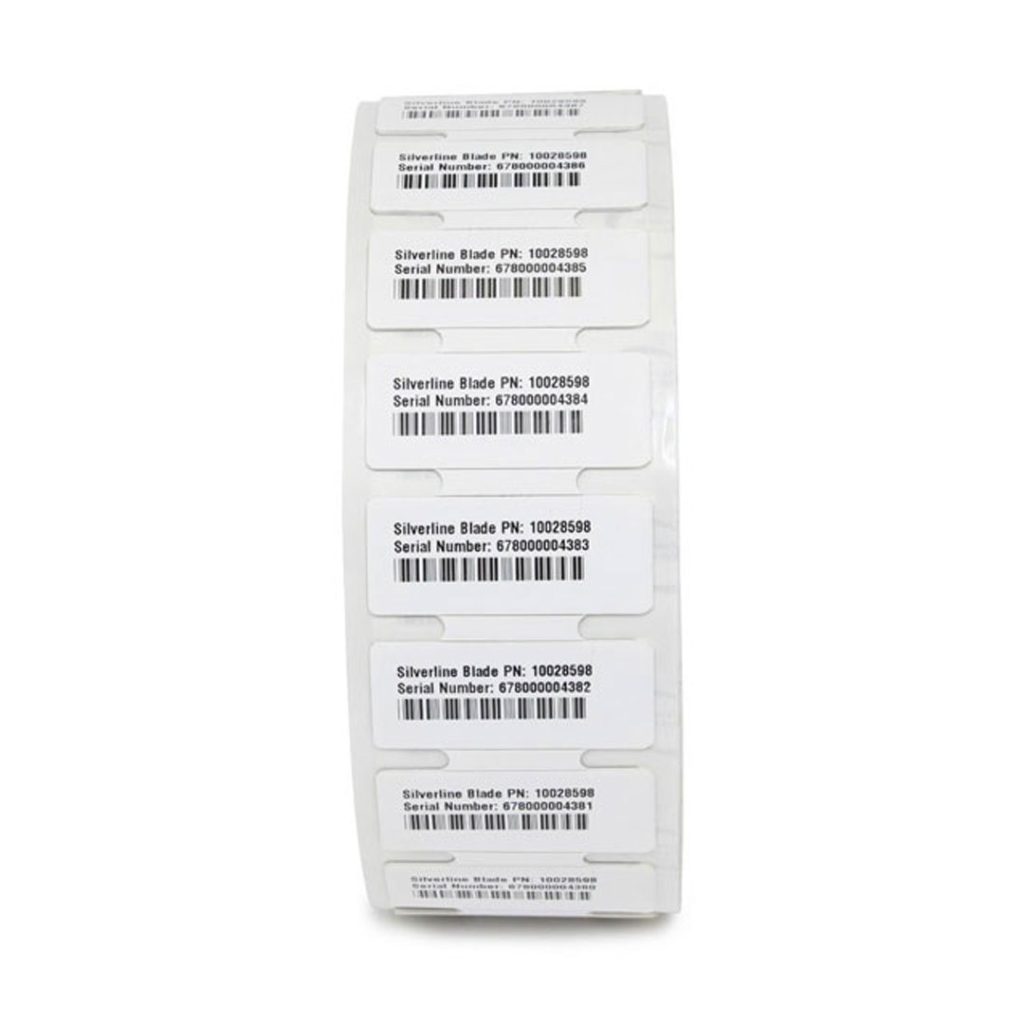
Silverline Blade Inlay RFID Label
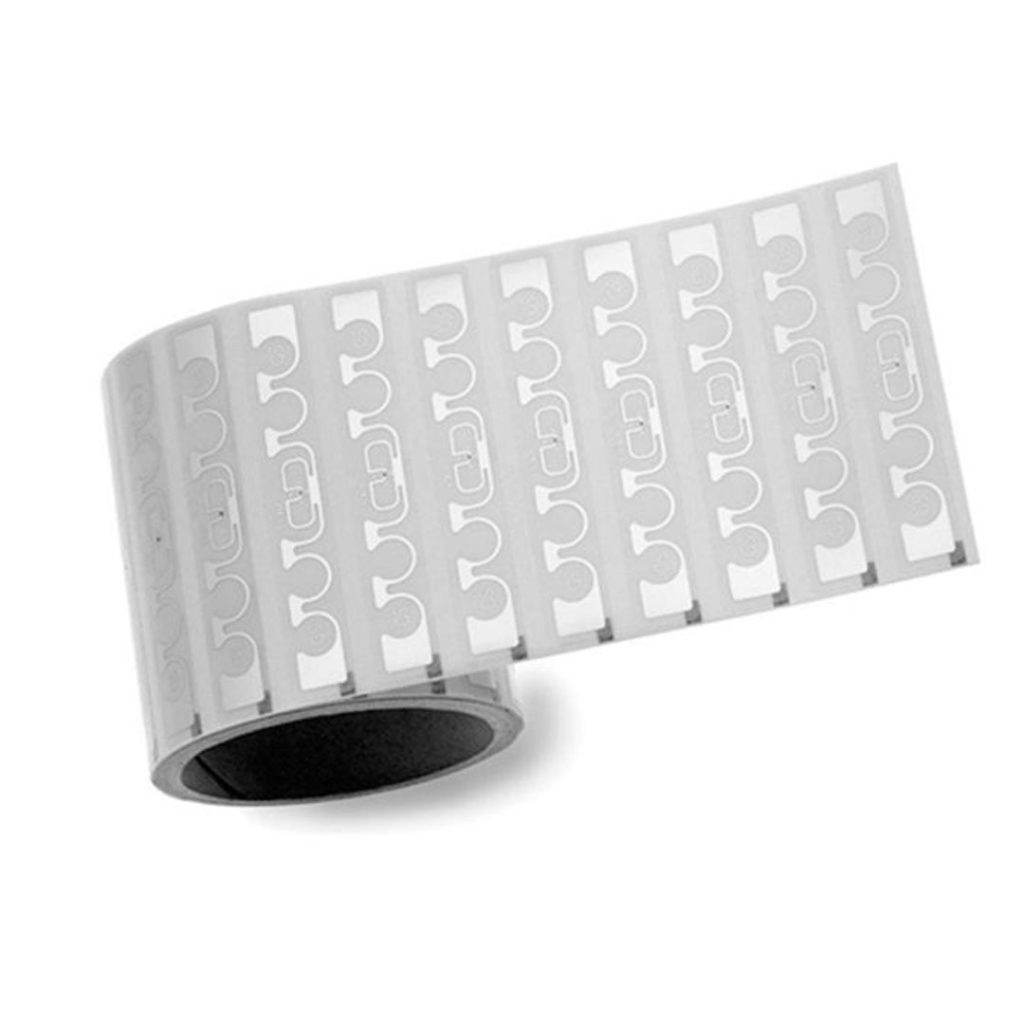
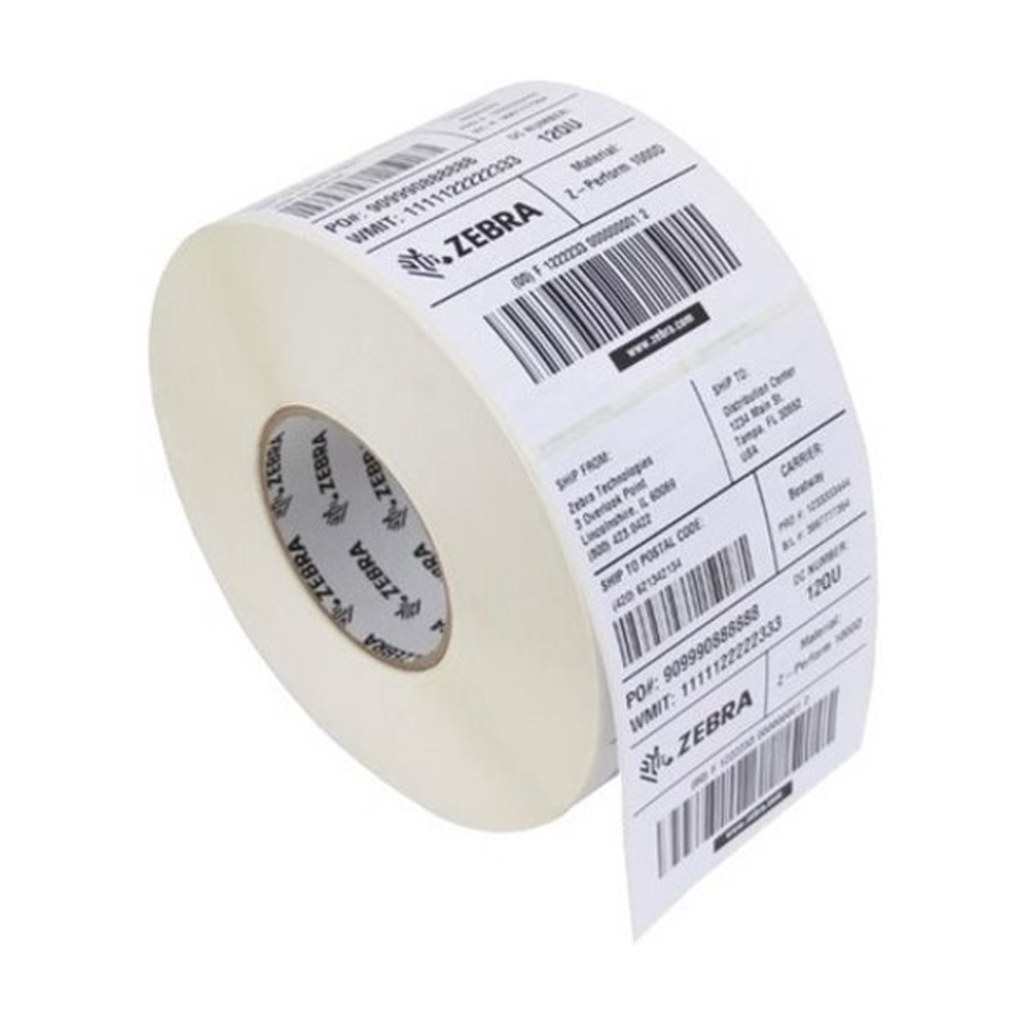
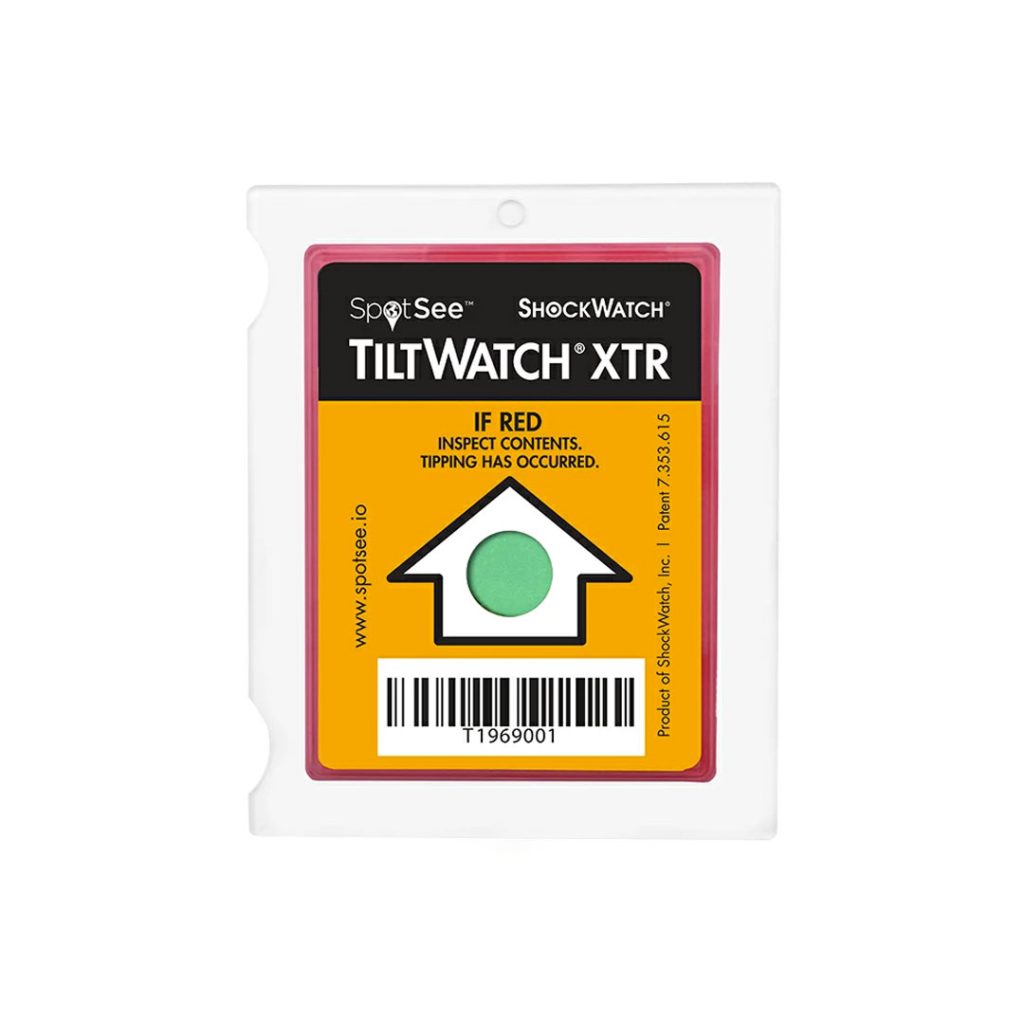
Forget fancy robots or complicated software – sometimes the most important things in a factory are the simplest. Take industrial labels, for instance. These aren’t your average price tags; they’re secret weapons for keeping your factory running smoothly, safely, and efficiently. This page dives into the power of industrial labeling, showing you how they can save you time, prevent accidents, and streamline your entire operation. We’ll tackle common challenges like peeling labels and worn-out warnings, then showcase how labels are used in different industries, from keeping track of tiny components to making sure final products have all the information they need. By the end of this page, you’ll see how industrial labels can be your secret weapon for a smoother, safer, and more efficient factory floor.
The importance of Industrial Labeling
In the fast-paced world of industrial manufacturing, efficiency, safety, and clarity are paramount. This is where industrial labeling comes into play. It might seem like a simple detail, but effective labeling is an essential cornerstone of any successful industrial operation.
Here’s why industrial labeling is so important:
- Enhanced Efficiency: Clear and concise labels can significantly improve workflow throughout your facility. By having important information readily available on pipes, machinery, and storage containers, employees can quickly identify what they need, reducing wasted time and confusion. This translates to increased productivity and overall efficiency.
- Improved Identification: Industrial labels ensure accurate identification of products, parts, materials, and equipment. This is crucial for maintaining proper inventory control, streamlining production processes, and ensuring components are used correctly. In Mexico, for instance, some industries may have specific regulations regarding product identification, and clear labeling can help ensure compliance.
- Safety and Hazard Prevention: Industrial environments can pose various safety hazards. Properly designed labels with clear warnings and hazard symbols can play a vital role in preventing accidents and injuries. They can communicate important information about potential risks, proper handling procedures, and necessary Personal Protective Equipment (PPE) requirements.
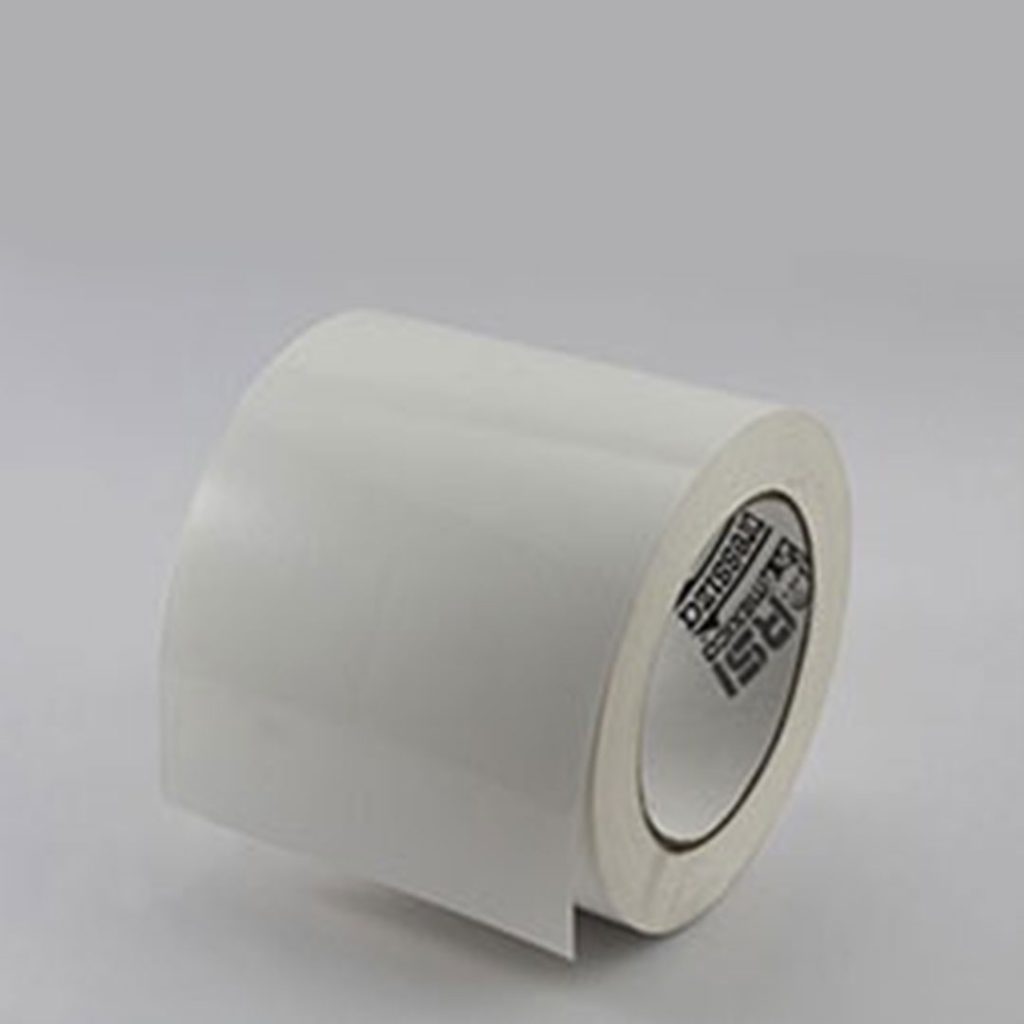
Etiqueta Material Pressiza I09 Papel
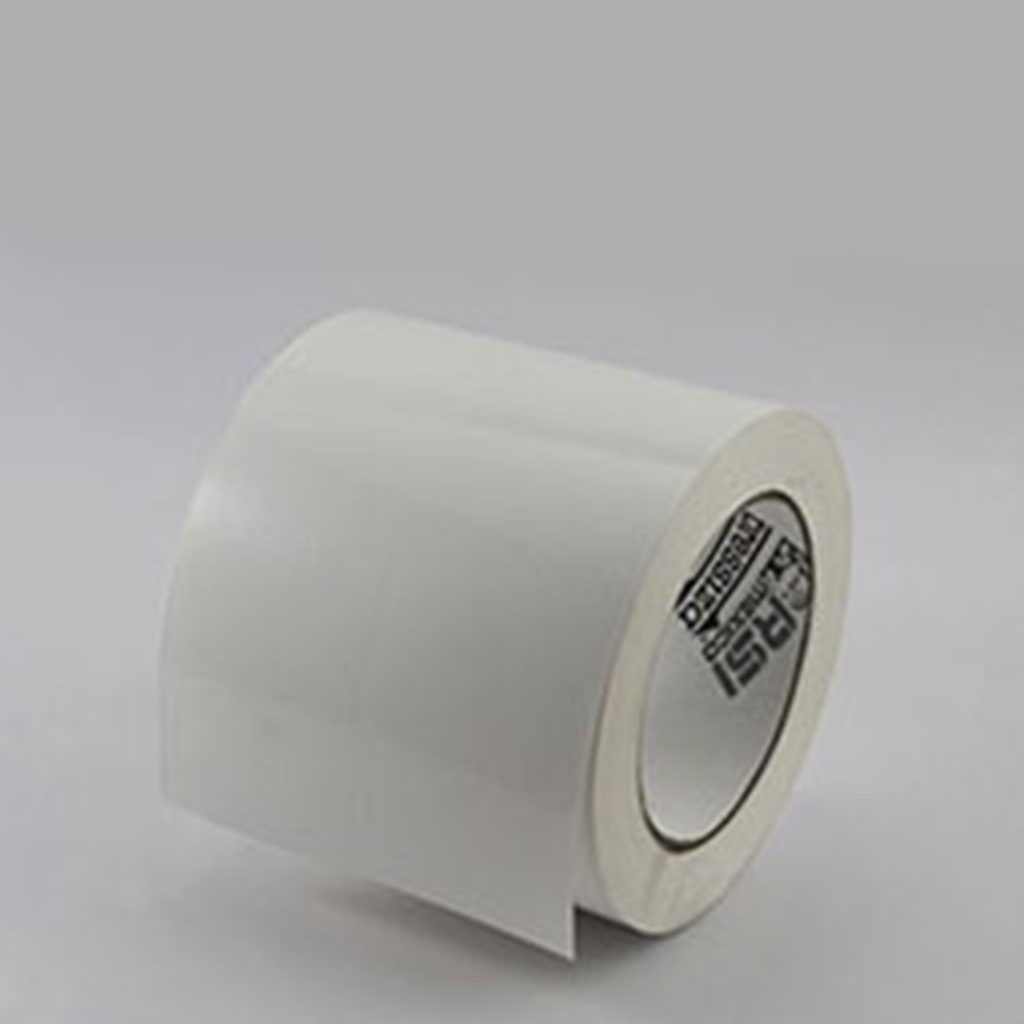
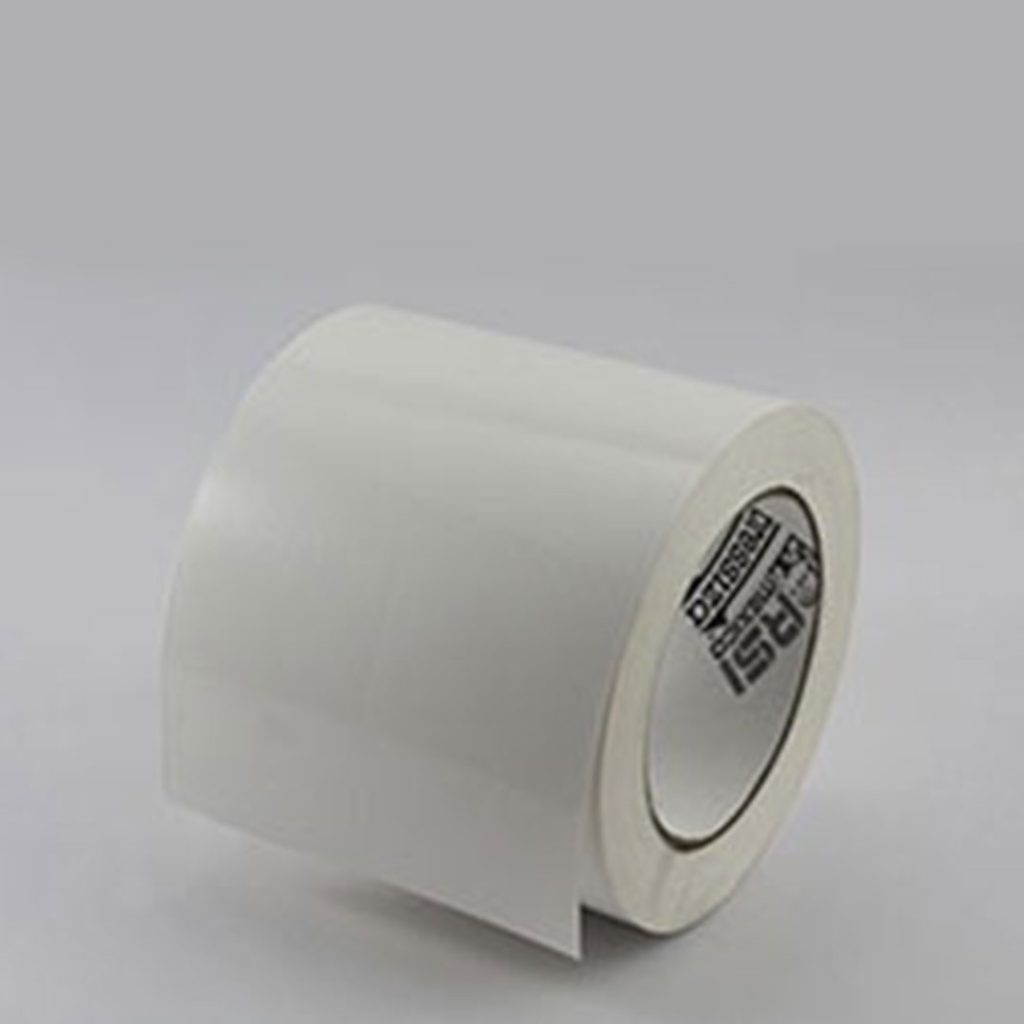
Etiqueta Material Pressiza I05 Papel
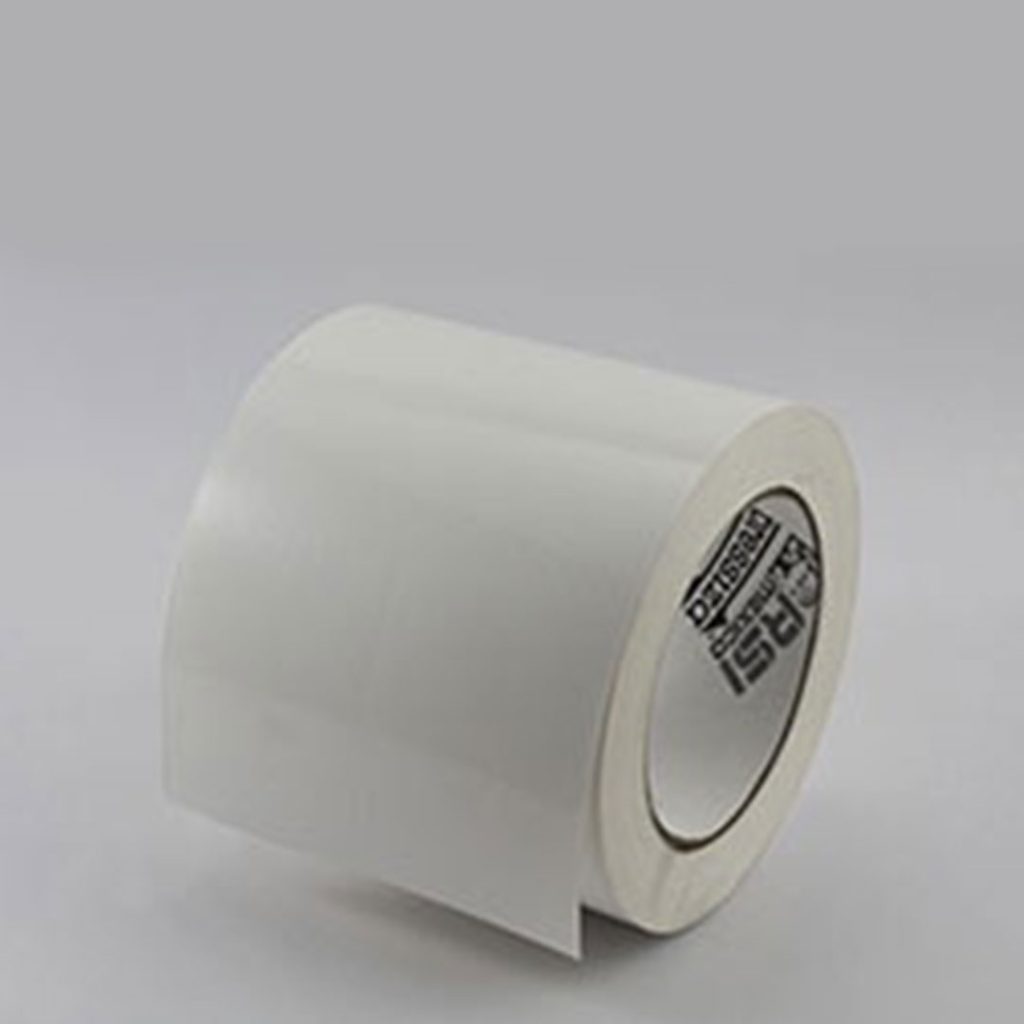
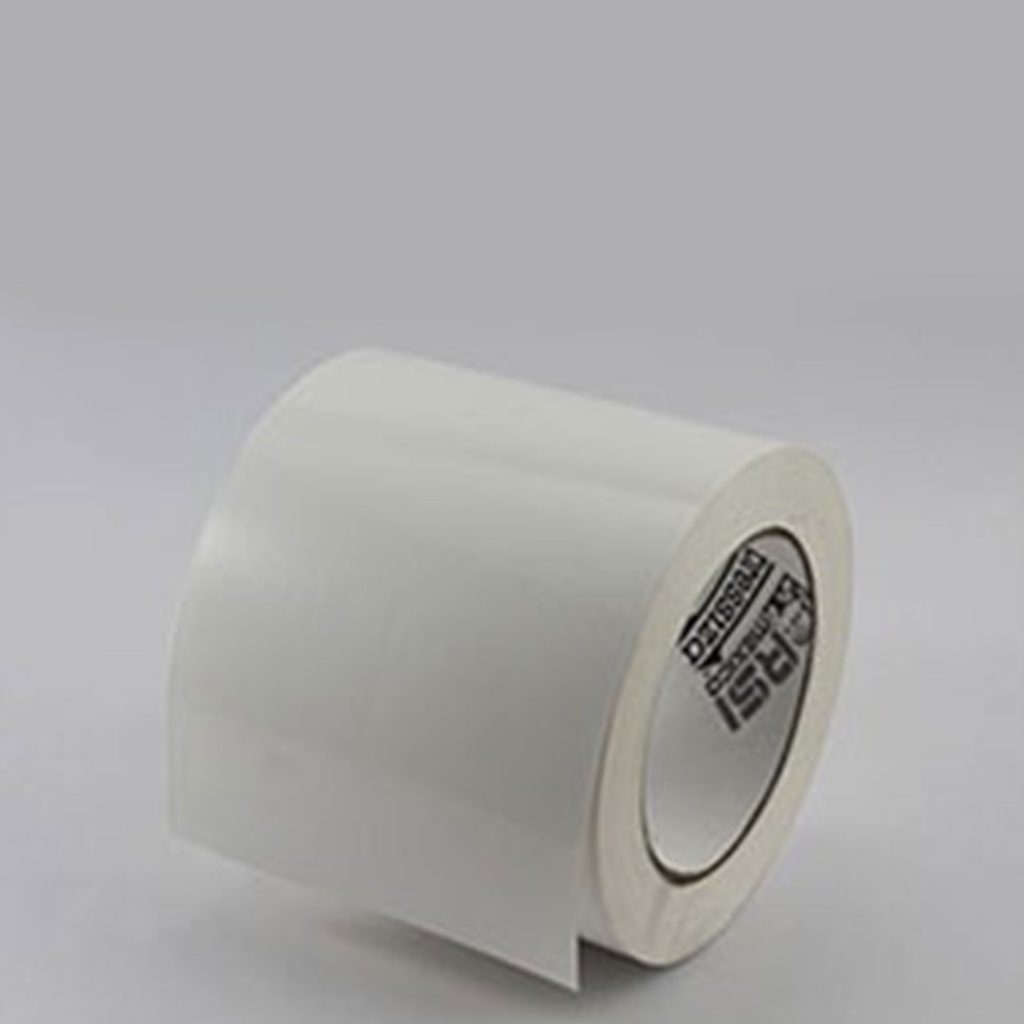
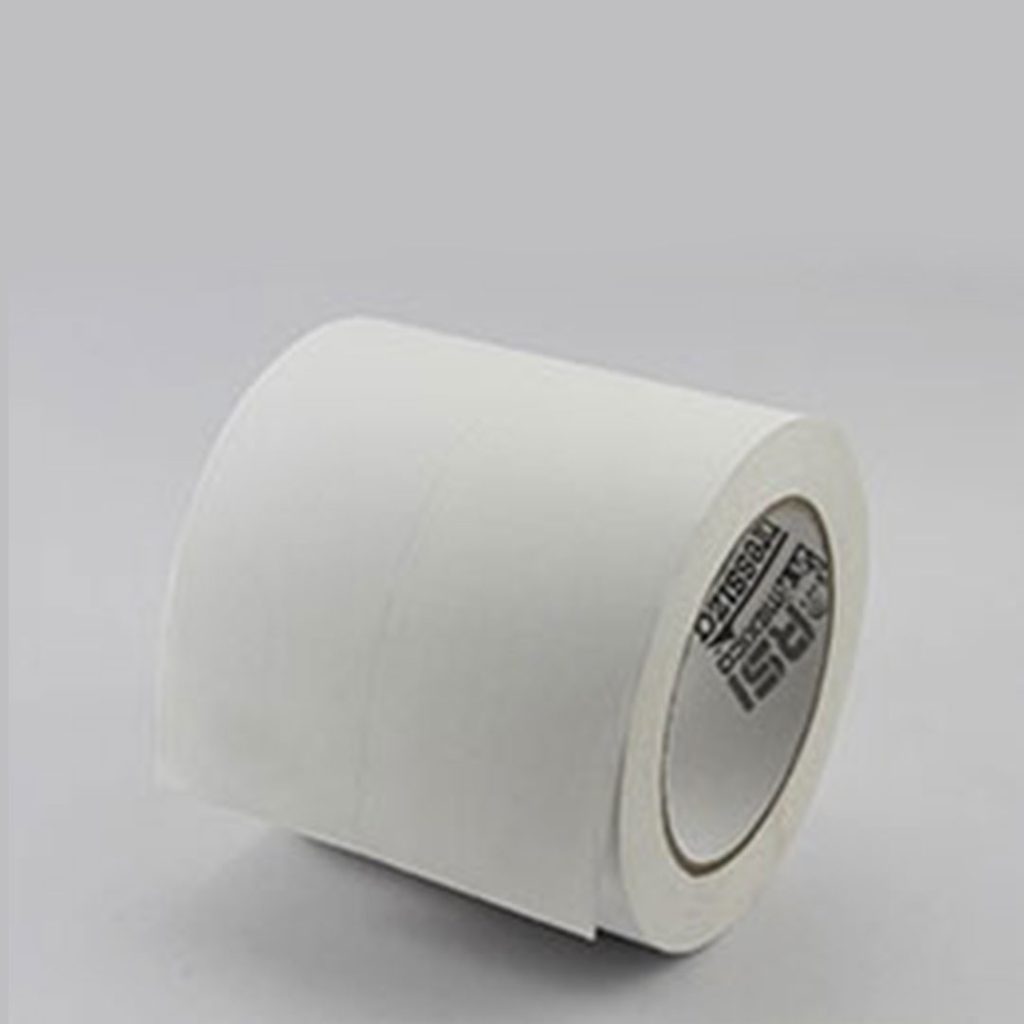
Common problems in industrial labeling
Even the most well-designed labeling system can encounter challenges. Here, we’ll discuss some common problems in industrial labeling and how to address them:
Label Detachment
One of the most frustrating issues is label detachment, where labels peel off or fall away from the intended surface. This can occur for several reasons:
- Improper Material Selection: Not all labels are created equal. Choosing a label material that isn’t compatible with the application environment is a recipe for detachment. For example, labels designed for room temperature might not adhere well to surfaces exposed to extreme cold in freezers.
- Surface Contamination: Dust, dirt, oil, or other contaminants on the application surface can prevent the adhesive from forming a strong bond. Ensuring a clean and dry surface before label application is crucial.
- Environmental Factors: Excessive heat, cold, moisture, or UV radiation can degrade the adhesive over time, leading to label detachment.
Solutions:
- Matching Technology to Application: The key to preventing label detachment lies in selecting the right labeling technology for the job. Industrial label suppliers offer a wide range of materials specifically designed to withstand harsh environments like freezers, high heat, or chemical exposure.
- Surface Preparation: Proper surface cleaning before label application is essential. This may involve using specific cleaning solutions or wipes to remove any contaminants that could hinder adhesion.
- Label Application Verification: In some cases, employing a label application verification system can be beneficial. These systems use sensors to ensure proper label placement and adhesion, minimizing the risk of detachment.
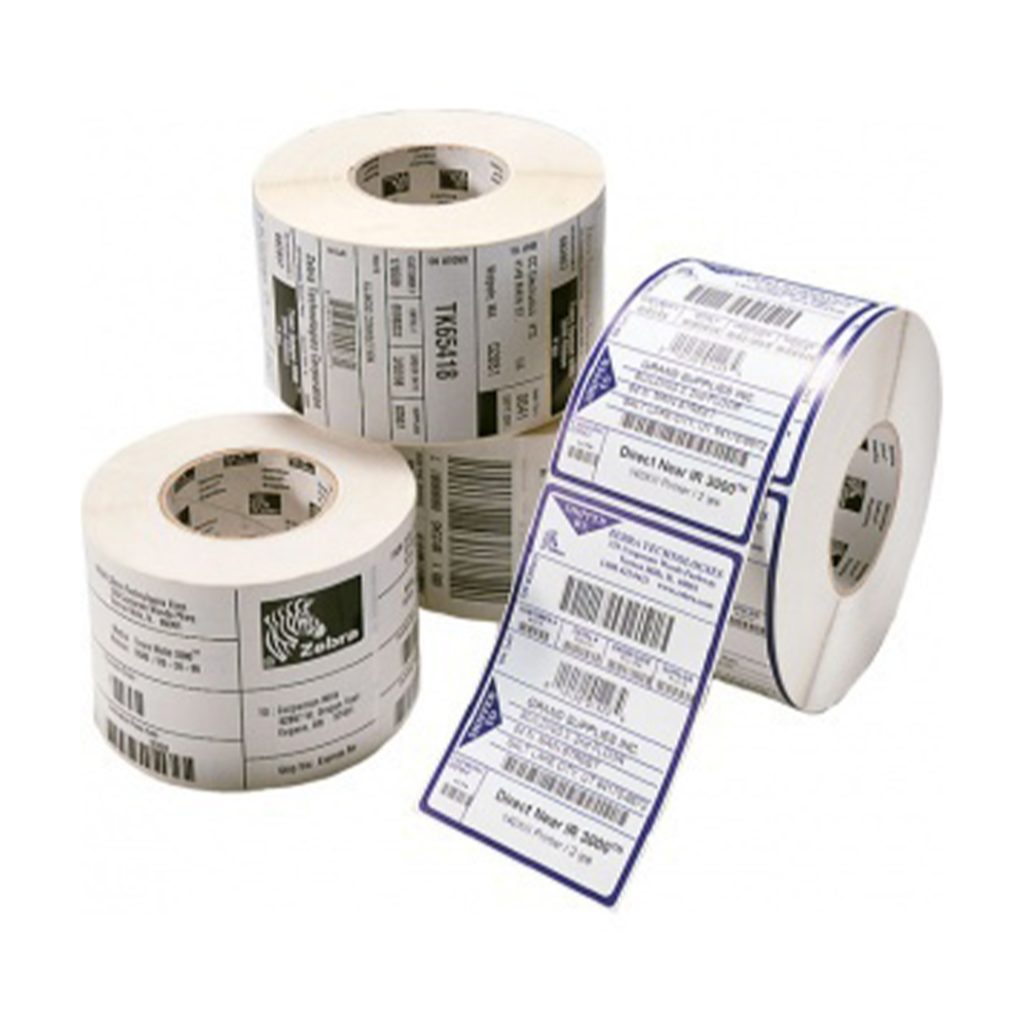
Etiqueta Z-Supreme 3000T White Label
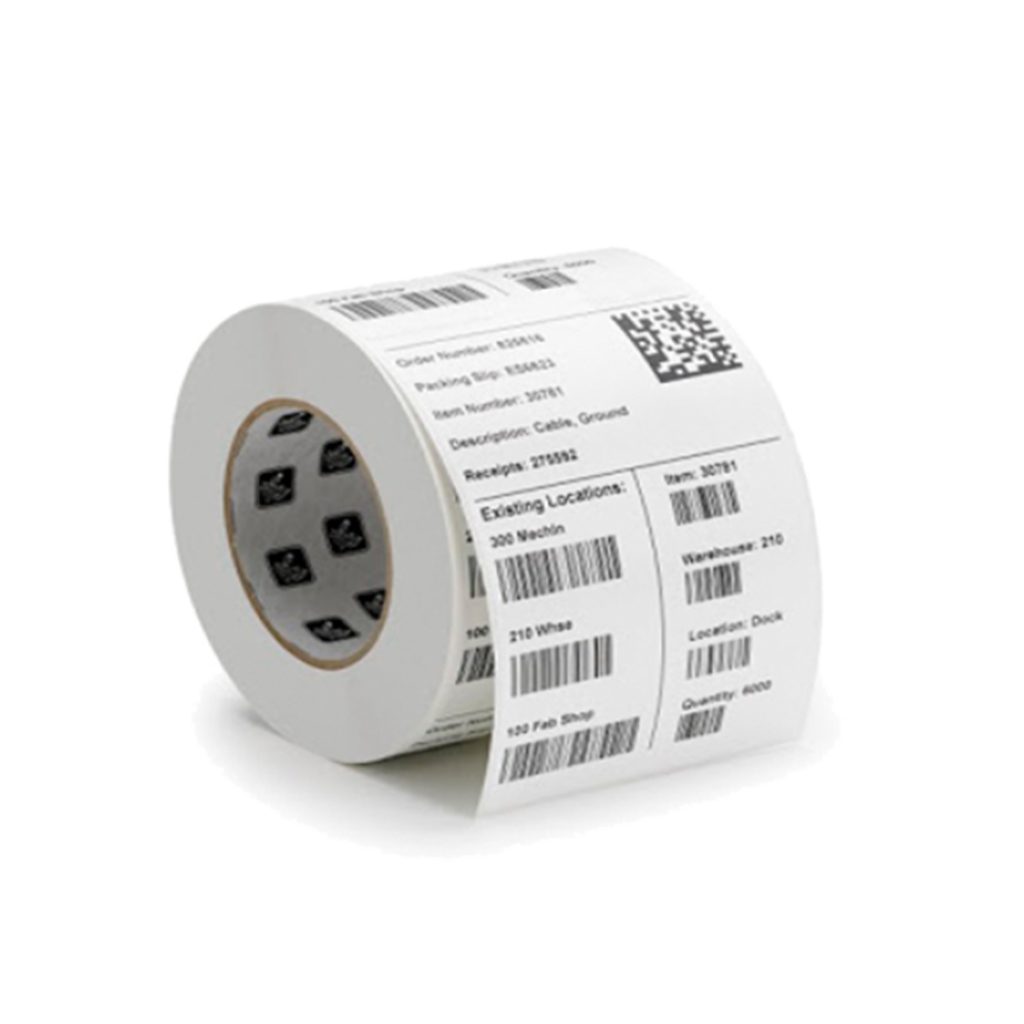
Etiqueta PolyO 4000T Label
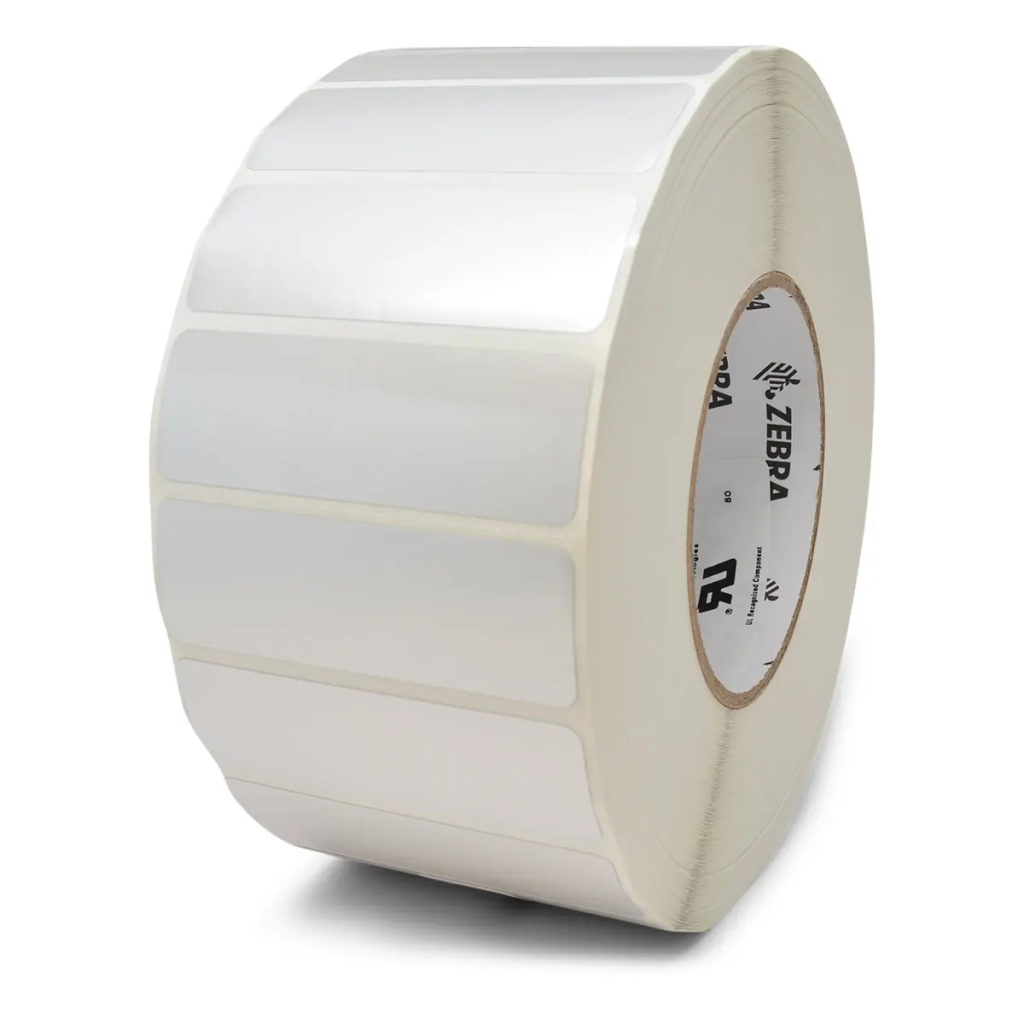
Etiqueta Z-Xtreme 4000T Silver Label
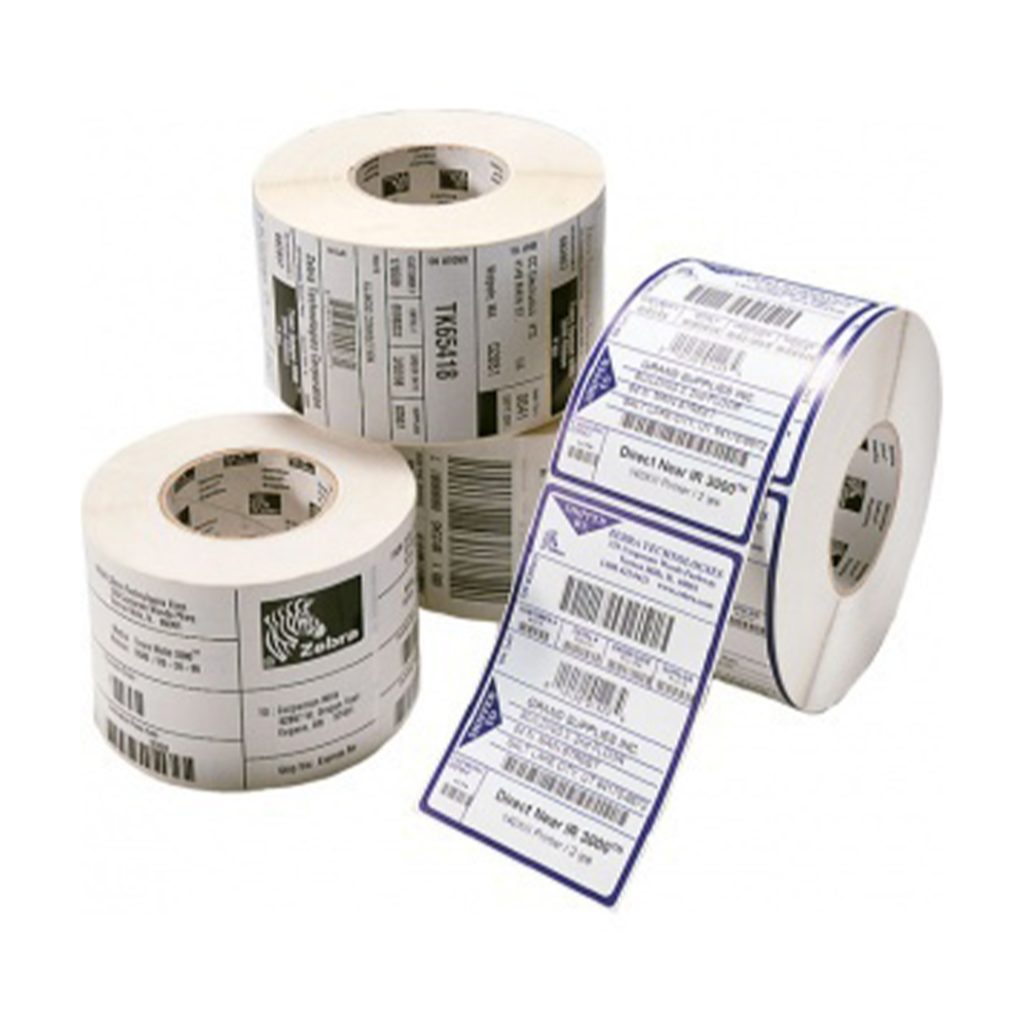
Etiqueta Z-Supreme 4000T Green Label
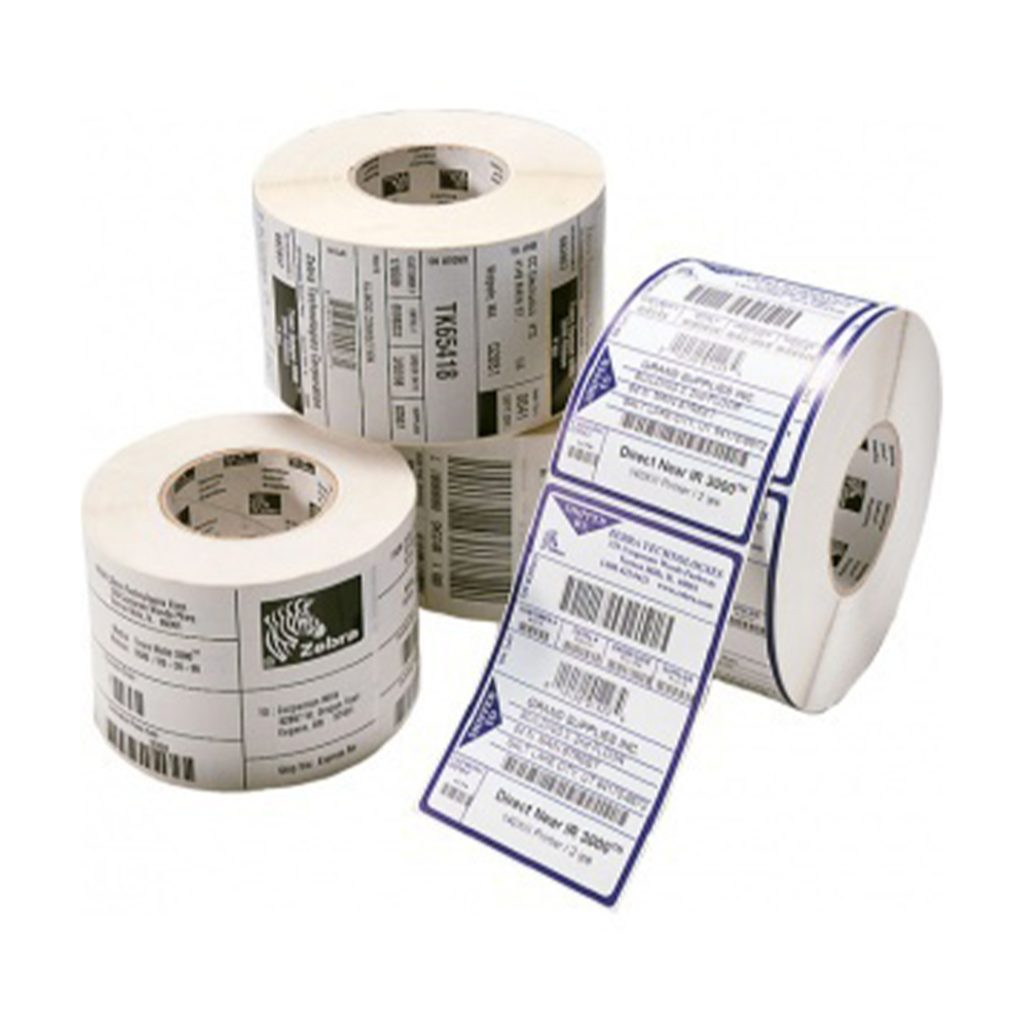
Etiqueta Z-Ultimate 4000T High-Tack Silver Label
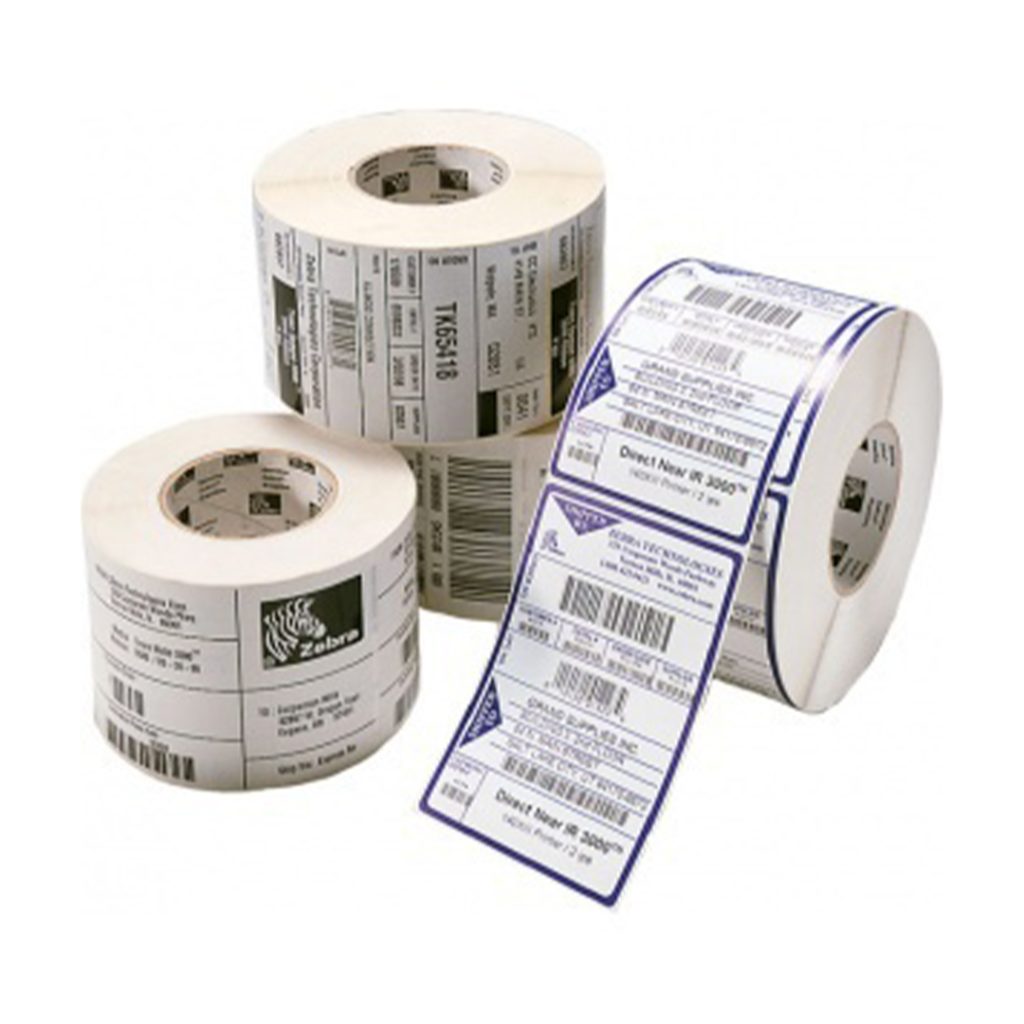
Etiqueta PolyPro 4000T Removable Label
Print degradation
Another common issue is print degradation, where the label’s text, barcodes, or images become faded, smeared, or illegible. This can have serious consequences, hindering product identification, safety communication, and regulatory compliance. Here’s what can cause print degradation:
- Exposure to Elements: Harsh environmental conditions like sunlight, UV rays, constant moisture, or extreme temperatures can break down the ink or toner used for printing. This can lead to fading, blurring, or complete loss of information on the label.
- Chemical Exposure: Certain chemicals used in industrial settings can react with the label material or ink, causing the print to deteriorate.
- Friction or Abrasion: Labels subjected to frequent rubbing or scraping against other objects can experience physical wear and tear, damaging the printed information.
Solutions:
- Durable Printing Technologies: Industrial label printing methods like thermal transfer or laser printing offer superior print durability compared to standard inkjet printing. These methods utilize heat or a laser to fuse the ink or toner with the label material, resulting in prints that are more resistant to fading, scratching, and chemicals.
- Protective Overlaminates: Applying a protective overlaminate to the label acts as a shield against environmental factors, chemicals, and physical abrasion. Overlaminates come in various thicknesses and finishes, providing additional protection while maintaining readability of the printed information.
- Ink and Material Selection: Choosing the right ink or toner formulation for the specific application environment can significantly enhance print durability. For instance, UV-resistant inks can be used for labels exposed to sunlight, while chemical-resistant inks are suitable for environments with harsh chemicals.
use cases of Industrial labeling
Tracing Components
Effective component tracking is crucial for maintaining quality control, managing inventory, and ensuring product safety. Industrial labeling empowers manufacturers to implement robust component tracing systems.
Importance:
- Enhanced Quality Control: By assigning unique identifiers to components through labeling, manufacturers can track them throughout the production process. This allows for pinpointing potential issues with specific batches or identifying defective components for corrective action.
- Improved Inventory Management: Component labels with relevant information like part numbers and lot codes facilitate efficient inventory control. It enables real-time tracking of stock levels, minimizing the risk of stockouts and optimizing ordering processes.
- Product Recalls and Safety: In the event of a product recall, component tracing through labels becomes essential. Manufacturers can quickly identify and isolate affected products, minimizing safety risks and potential customer harm.
Challenges:
While component tracing offers significant benefits, implementing a robust system comes with its own set of challenges. Different manufacturing processes present unique obstacles when it comes to label selection and adhesion.
- Metal Stamping: Components formed through metal stamping can be oily, which can hinder label adhesion. Special label materials with strong adhesives designed for oily surfaces are necessary.
- Plastic Injection Molding: Plastics used in injection molding can have varying surface energies, impacting label adhesion. Additionally, parts may shrink slightly after molding, potentially causing label distortion. Choosing labels with compatible adhesives and considering shrinkage factors during label design are crucial. Release agents used in the molding process can also affect adhesion, so selecting labels compatible with these agents is important.
- Painting: Labels applied to components undergoing painting processes like cataphoresis (electrodeposition) need to withstand high temperatures in ovens. Special heat-resistant labels are essential in such applications.
- Chemical Treatments: Components undergoing cleaning, finishing, or other chemical treatments may require labels resistant to the specific chemicals used. Chemical-resistant inks and materials are necessary to ensure the label information remains intact.
- Electronics Manufacturing: Electronic components often encounter high temperatures during soldering and other processes. Labels designed for high-temperature environments are crucial to prevent degradation. Additionally, some electronic components may be destined for use in tropical climates. “Tropicalized” labels with enhanced moisture resistance are necessary for such applications.
- Autoclave Sterilization: Components requiring sterilization in autoclaves (high-pressure steam chambers) necessitate labels that can withstand extreme temperatures and moisture.
- Salting: Components used in applications involving salt exposure, like food processing equipment, require labels with strong adhesion that resist erosion from salt and other potential oils or shocks.
- Metal Forming: Labels applied to components undergoing high-temperature metal forming processes need to be heat-resistant to maintain adhesion and legibility.
By understanding the specific challenges of each manufacturing process, selecting the appropriate labeling technology and materials becomes paramount for successful component tracing.
Industry Examples:
- Automotive Industry: Every car component, from engines to airbags, carries critical safety implications. Labeling with unique identifiers allows automakers to track components across the supply chain, ensuring quality and enabling targeted recalls if necessary.
- Electronics Industry: Electronic components are often intricate and can be sourced from various suppliers. Labeling with detailed information like part numbers and manufacturing dates facilitates traceability, allowing for troubleshooting malfunctions and identifying potential counterfeit parts.
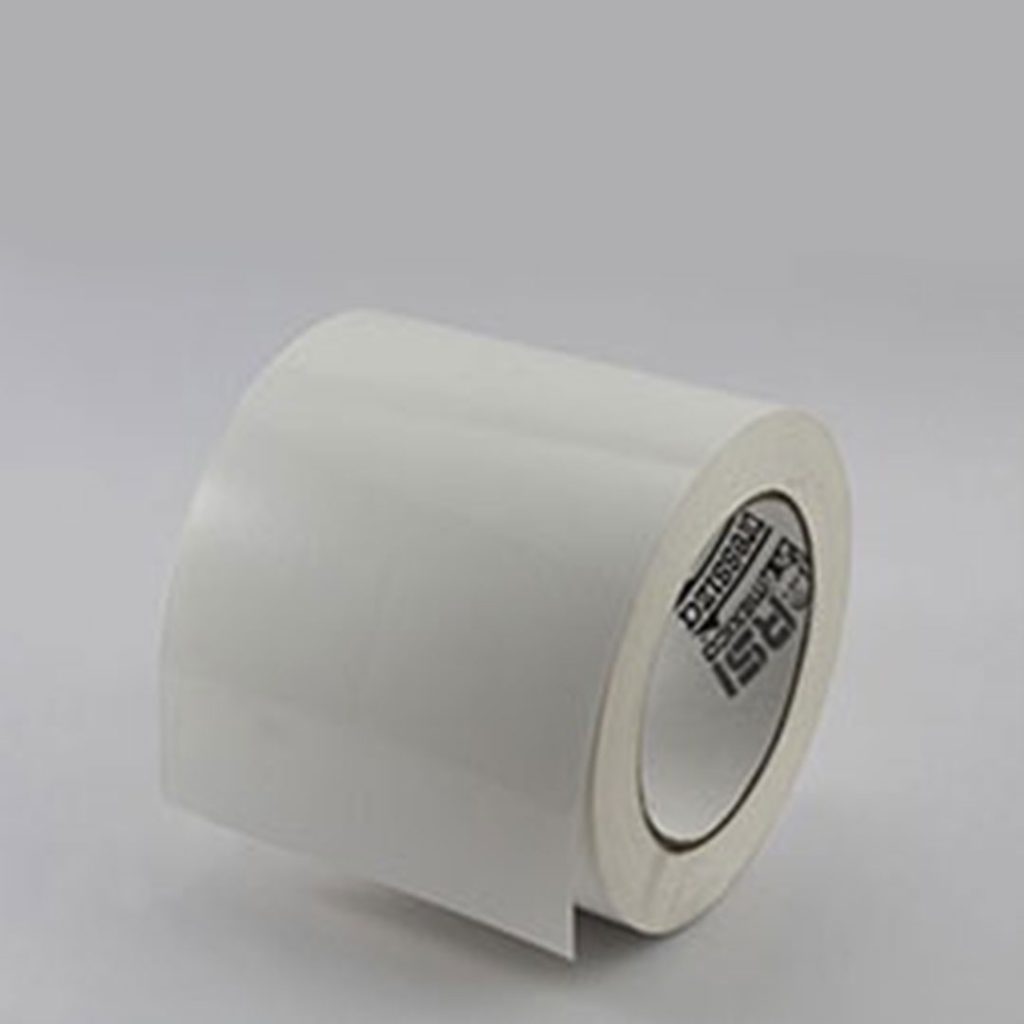
Etiqueta Material Pressiza I09 Papel
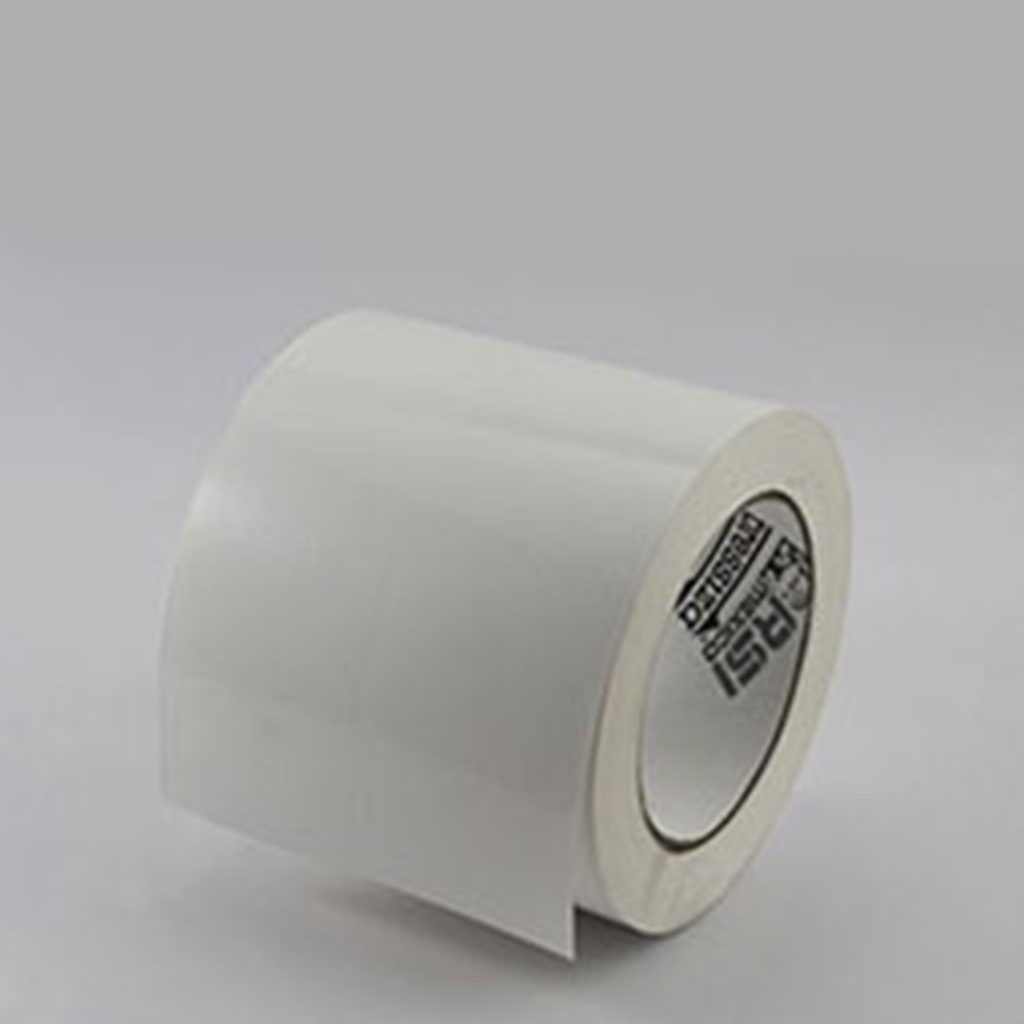
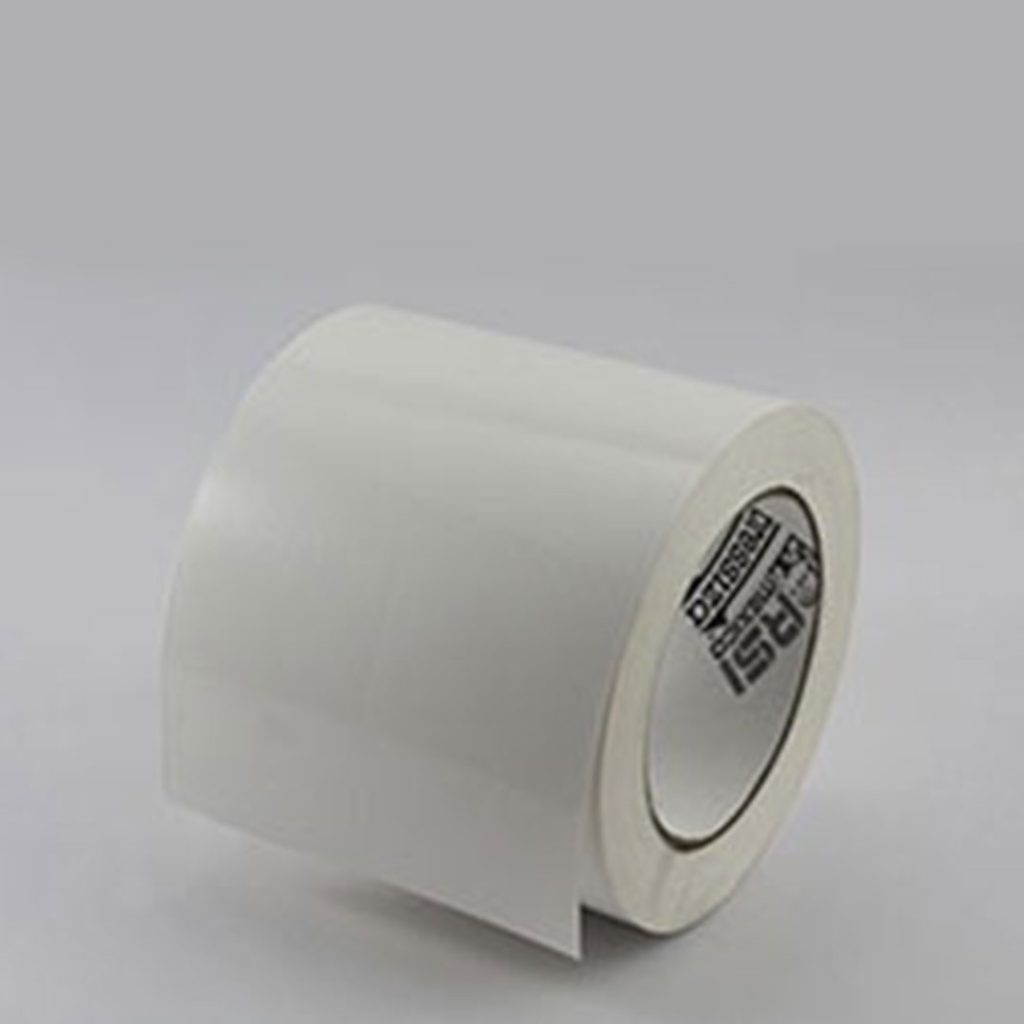
Etiqueta Material Pressiza I05 Papel
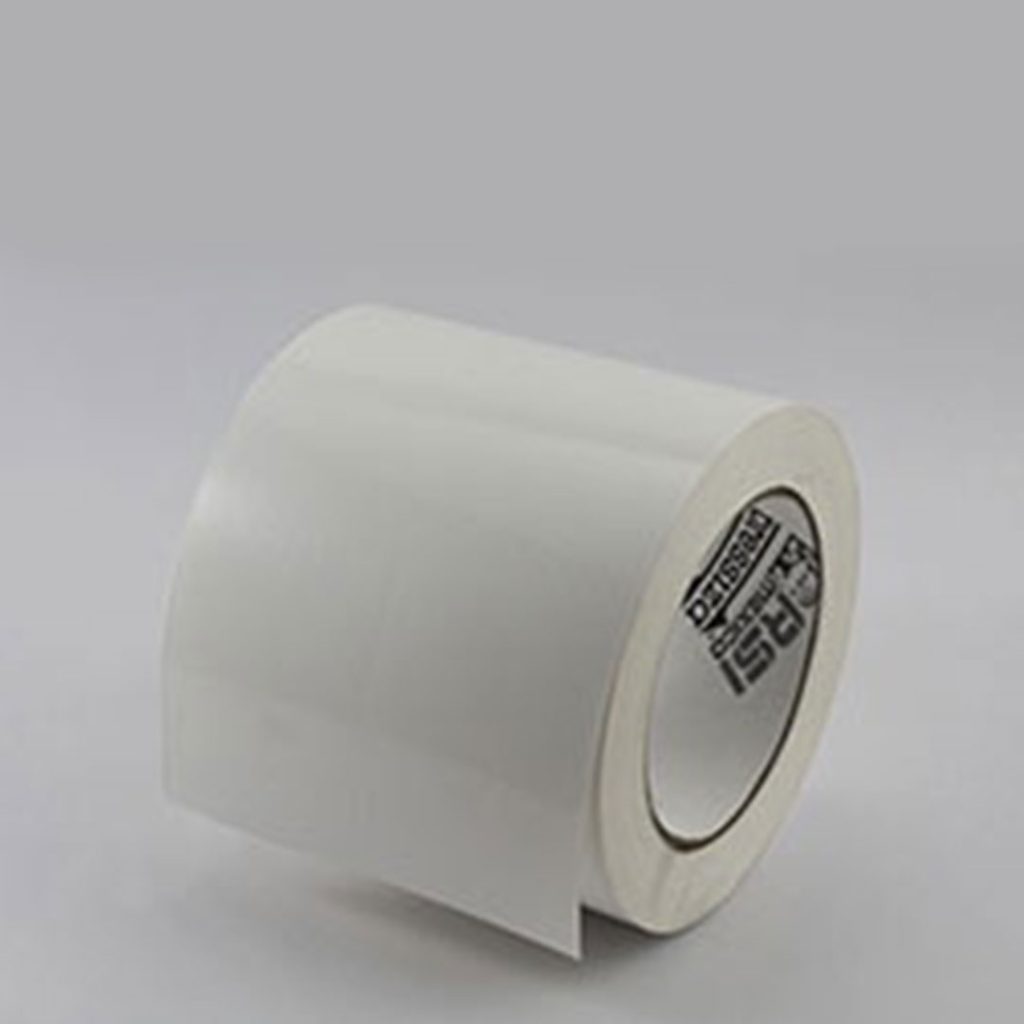
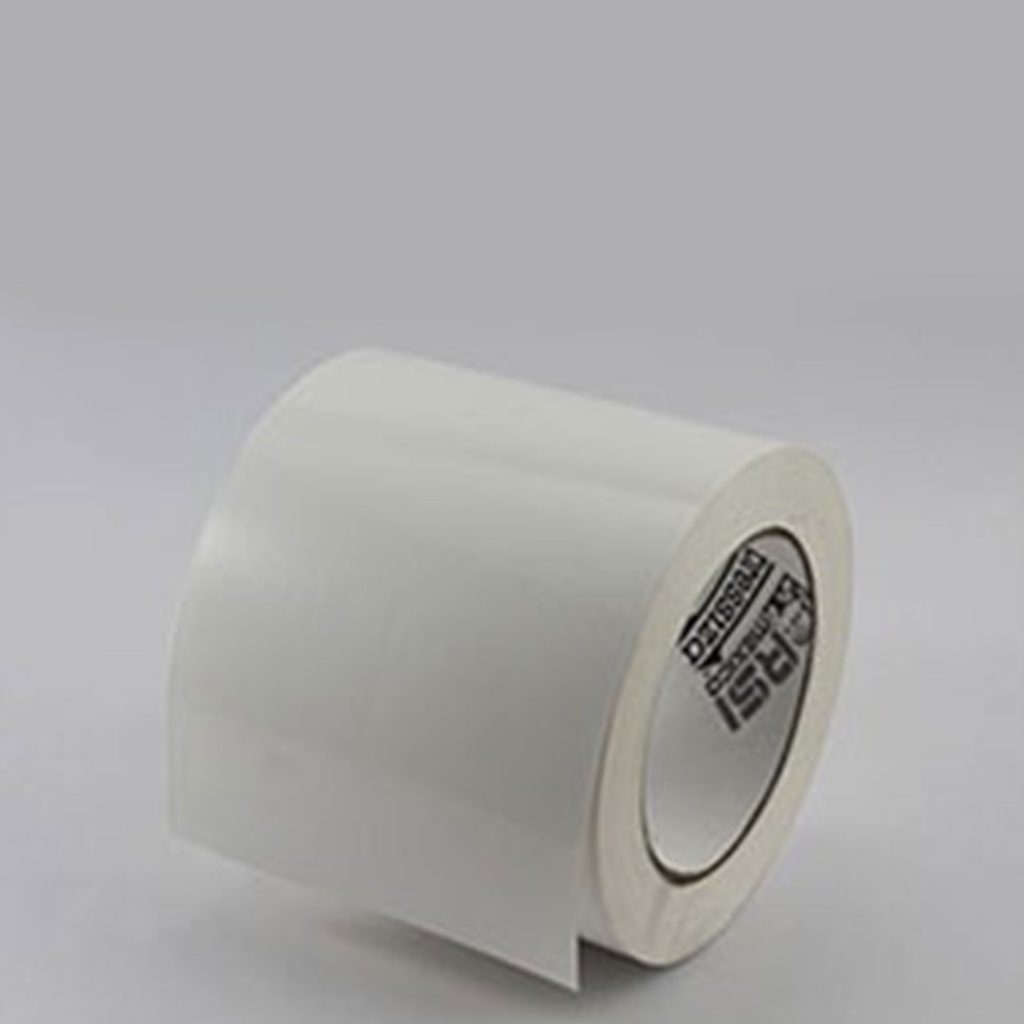
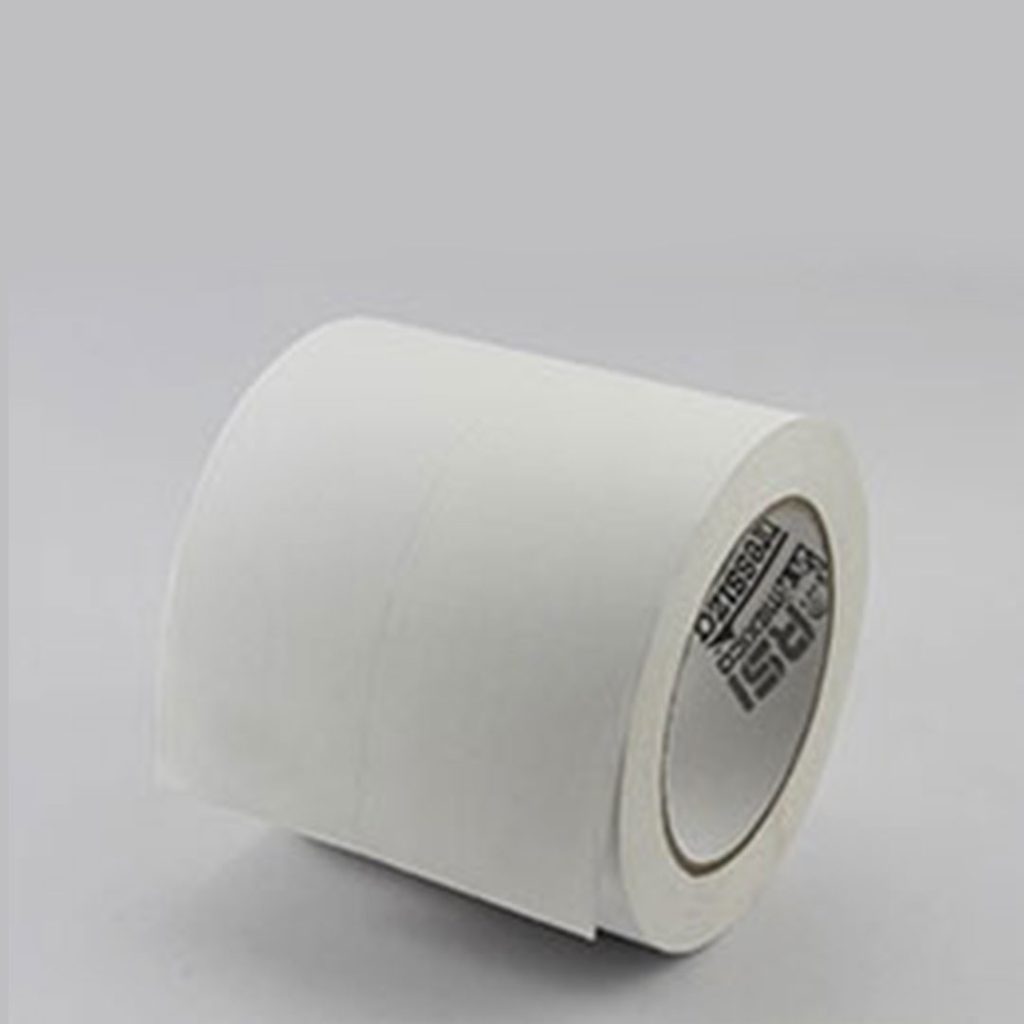
Identification of final products
Beyond component tracking, industrial labels play a critical role in final product identification. This involves providing essential information directly on the finished product itself.
Importance:
- Clarity and Accuracy: Clear and accurate product identification ensures customers receive the correct item. Labels display vital information like product name, model number, serial number, and manufacturing date.
- Regulatory Compliance: Many industries have specific regulations regarding product labeling. For instance, labels may need to include safety warnings, hazard symbols, or disposal instructions based on the product’s content or function.
- Improved Traceability: Product labels with unique identifiers like barcodes or QR codes facilitate traceability throughout the supply chain. This allows manufacturers to track product movement, identify potential counterfeits, and streamline recall processes if necessary.
Challenges:
Just like with component tracing, final product labels need to withstand the rigors of the product’s intended use environment. Here are some factors to consider:
- Weathering (UV): Products exposed to sunlight require UV-resistant labels to prevent information fading over time.
- High/Low Temperatures: Labels need to adhere and remain legible in extreme hot or cold conditions, depending on the product’s application.
- Exposure to Chemicals: Products used in environments involving chemicals like alcohol, hexane, brake fluid, or lubricants necessitate labels resistant to those chemicals. The specific chemicals encountered will dictate the choice of label material and ink.
- Mechanical Resistance: Products subjected to physical wear and tear, like shocks, friction, or scratches, require labels with strong adhesion and abrasion resistance.
- Resistance to Humidity (Saline Environment): Products used in humid or saline environments, like marine equipment, need labels that can withstand moisture and salt exposure without degrading.
Use cases:
- Food and Beverage Industry: Food and beverage packaging relies heavily on clear and compliant labeling. Labels display product information like ingredients, nutritional facts, expiration dates, and any potential allergens. These labels also often include barcodes for efficient tracking and inventory management. Since food packaging may encounter moisture, condensation, or even refrigeration, label materials and adhesives need to be resistant to such conditions.
- Medical Device Manufacturing: Medical devices require clear labels for patient safety. These labels display vital information and need to withstand sterilization processes to ensure the information remains legible. The right labeling solutions are crucial for clear communication and proper use of medical devices.
Work and machinery equipment
Industrial labels play a vital role in ensuring safety and smooth operation of machinery and equipment. Here’s how:
- Safety and Hazard Prevention: Clearly labeled machinery with warnings and pictograms can prevent accidents and injuries. Labels can highlight potential hazards, mandatory Personal Protective Equipment (PPE) requirements, and proper lockout/tagout procedures.
- Instructional Labeling: Machinery operation instructions displayed on labels can guide operators on proper use, minimizing errors and maximizing efficiency.
- Environmental Durability: Labels need to withstand the specific environment of the machinery. This could involve resistance to extreme heat or cold, exposure to steam, chemicals, or UV radiation depending on the application.
Industrial labels find use across various types of machinery and equipment, from construction tools and factory assembly lines to power generators and medical devices. Selecting the right label material and design ensures clear communication, operator safety, and optimal equipment function.
Valves, drains, filters, pumps, hoses
Maintaining a safe and efficient operation relies heavily on clear identification and proper labeling of essential components like valves, drains, filters, pumps, and hoses. Here’s why labeling is crucial:
- Improved Flow Control and Maintenance: Clearly labeled valves with flow direction indicators prevent accidental closure of the wrong line, ensuring proper flow control throughout the system. Labels on filters and drains can indicate recommended service intervals, facilitating timely maintenance and preventing equipment failures.
- Safety and Hazard Communication: Pumps handling hazardous materials require clear labels with hazard symbols and appropriate warnings. This helps prevent accidents and ensures operators take necessary safety precautions.
- Durability in Harsh Environments: Labels on these components need to withstand the specific conditions they encounter. For instance, labels near hot pipes require heat resistance, while those in freezers need to withstand extreme cold without cracking or peeling. Chemical-resistant labels are crucial for components exposed to corrosive liquids or cleaning agents.
By employing the right labeling solutions, industrial facilities can ensure clear communication, promote safe operation of these critical components, and optimize overall system performance.
Cables and conductors
Clear labels are vital for cables in industrial settings. They simplify installation and maintenance, enhance safety by highlighting voltage or hazards, and improve organization within electrical systems. Choosing the right labels involves considering temperature extremes, potential chemical exposure, and abrasion resistance to ensure long-lasting performance in harsh environments.
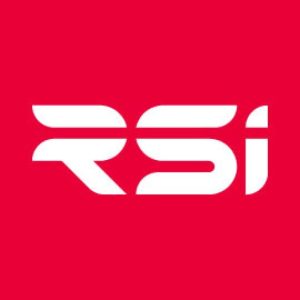
Lior Rubin
Socio Estratégico RSI Mexico